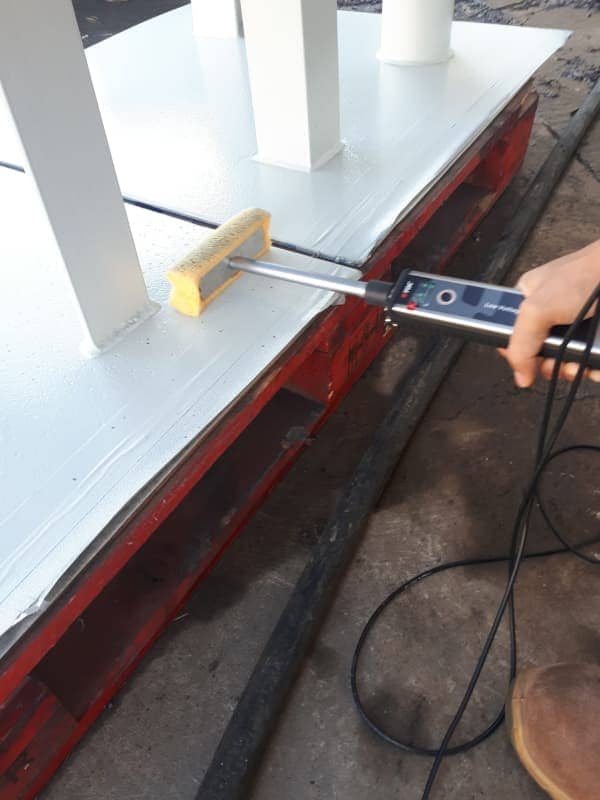
PAINTING SERVICES
-
INTRODUCTION Over time, corrosion can produce alterations in the structural characteristics of metal components that also compromise safety and functionality. An effective management of the corrosion protection process is therefore essential to guarantee quality and continuity of the service and for the reduction of direct and indirect costs deriving from maintenance interventions, including among them also the interruptions of the services for which the components are intended. Since July 2014, the structural carpentry sector has been regulated through the EN1090-1 standard, harmonized with the European Regulation No. 305/2011 for construction products. The standard defines “durability” of the components as an essential performance for the use of these products and refers to the requirements defined in EN12944 as mandatory legislation for the application of coatings by painting. The Oil & Gas sector is also concentrating its attention on the control of corrosion protection processes with the aim of improving the reliability and efficiency of the equipment during their useful life.
- Inspections / Controls and Tests on Surface Preparation “BLASTING INSPECTION” in accordance with the technical specifications and main standards UNI EN ISO 8501-1, UNI EN ISO 8501-3, UNI EN ISO 8503-1, UNI EN ISO 12944-4
- Inspections / Controls and Tests during and upon completion of the painting cycle in accordance with the technical specifications and main standards UNI EN ISO 12944-1, UNI EN ISO 12944-2, UNI EN ISO 12944-3, UNI EN ISO 12944 -4, UNI EN ISO 12944-5, UNI EN ISO 12944-7, UNI EN ISO 12944-8, UNI EN ISO 1090-2 Par.10 + App.F
- Inspections / Controls and Tests on REFERENCE AREAS / TEST SAMPLES. These areas allow to establish a minimum level of Quality in the realization of the painting cycle and also guarantee the truthfulness of the data provided and recorded. The Inspections and Controls will be carried out over the entire painting cycle to be treated, this consists of:
- Pre-Blasting Inspection (inspection of the surface to be treated before the sandblasting process)
- Blasting Inspections (inspections and tests on the entire blasting process)
- Painting application (presence at all painting phases pre / during / post application of the individual layers foreseen by the painting cycle.
- Recording of all the parameters found and issue of the Inspection Report
The inspections on suppliers consist in attending the tests carried out at the suppliers, during production and in the subsequent phases. They allow to verify compliance with the requirements of the applicable international standards or technical specifications indicated in the contract, before the products are delivered to the customer. The painting inspector will attend the main stages of the Quality Control Plan and immediately issue the related inspection report. This service also allows you to identify any defects at the source and check in advance the specifications requested by the customer in order to eliminate or minimize the risk of additional costs due to deficiencies highlighted later on the site.
Supplier qualification consists in the adoption of a rating based on objective and impartial criteria, in order to ensure maximum transparency, objectivity and equal treatment for candidate companies. The service emerges from the need to assess in advance whether a potential supplier is able to complete purchase orders on term according to stable terms or if it can be taken into consideration for future tenders or to establish new relationships.
- Preparation of painting specifications;
- Manufacturing plans;
- “PFC” check;
- “ITP” Inspection and test Plan related to Surface Protection activities
Qualified inspectors in the field of corrosion protection will carry out supervision and control activities and provide specialized technical advice for all surface preparation activities, application of paints to protective coatings in general (hot galvanizing, painting, etc …)
- INFRARED THERMOHYGROMETER, for the measurement of Temperature, Humidity and Dew Point;
- BRESLER TEST KIT, for the verification of contaminating elements such as chlorides dissolved in water and any corrosion products in accordance with EN ISO 8502-6, EN ISO 8502-9
- Check after “dusting” on the sandblasted surface with Adhesive Tape, in accordance with UNI EN ISO 8502-3
- Test with “METHYL ETHYL KETONE”, for the control of Reticulation according to ASTM D4752 standard
- ISO COMPARATOR “GRIT”, for visual-tactile control of the profile of the sandblasted surface (Roughness) in accordance with UNI EN ISO 8503-2, 8503-1,12944-4
- ROUGHNESS CHECK, for checking the roughness of the sandblasted surface in Ra, Rz, Ry
- CHECK DEGREE OF CLEANLINESS, through comparison between Photographic standards in accordance with ISO 8501-1
- WET FILM THICKNESS CHECK, in accordance with UNI EN ISO 2808
- DRY FILM THICKNESS GAUGE, in accordance with UNI EN ISO 2808, ISO 19840
- “X TEST” ADHESION TESTS in accordance with ASTM D3359
- PIG “Painting Inspector Gauge”, destructive test for the control of the thickness of the single coating on a complete Painting cycle.
- Inspections / Controls and Tests on Surface Preparation “BLASTING INSPECTION” in accordance with the technical specifications and main standards UNI EN ISO 8501-1, UNI EN ISO 8501-3, UNI EN ISO 8503-1, UNI EN ISO 12944-4
- Inspections / Controls and Tests during and upon completion of the painting cycle in accordance with the technical specifications and main standards UNI EN ISO 12944-1, UNI EN ISO 12944-2, UNI EN ISO 12944-3, UNI EN ISO 12944 -4, UNI EN ISO 12944-5, UNI EN ISO 12944-7, UNI EN ISO 12944-8, UNI EN ISO 1090-2 Par.10 + App.F
- Inspections / Controls and Tests on REFERENCE AREAS / TEST SAMPLES. These areas allow to establish a minimum level of Quality in the realization of the painting cycle and also guarantee the truthfulness of the data provided and recorded. The Inspections and Controls will be carried out over the entire painting cycle to be treated, this consists of:
- Pre-Blasting Inspection (inspection of the surface to be treated before the sandblasting process)
- Blasting Inspections (inspections and tests on the entire blasting process)
- Painting application (presence at all painting phases pre / during / post application of the individual layers foreseen by the painting cycle.
- Recording of all the parameters found and issue of the Inspection Report
The inspections on suppliers consist in attending the tests carried out at the suppliers, during production and in the subsequent phases. They allow to verify compliance with the requirements of the applicable international standards or technical specifications indicated in the contract, before the products are delivered to the customer. The painting inspector will attend the main stages of the Quality Control Plan and immediately issue the related inspection report. This service also allows you to identify any defects at the source and check in advance the specifications requested by the customer in order to eliminate or minimize the risk of additional costs due to deficiencies highlighted later on the site.
Supplier qualification consists in the adoption of a rating based on objective and impartial criteria, in order to ensure maximum transparency, objectivity and equal treatment for candidate companies. The service emerges from the need to assess in advance whether a potential supplier is able to complete purchase orders on term according to stable terms or if it can be taken into consideration for future tenders or to establish new relationships.
- Preparation of painting specifications;
- Manufacturing plans;
- “PFC” check;
- “ITP” Inspection and test Plan related to Surface Protection activities
Qualified inspectors in the field of corrosion protection will carry out supervision and control activities and provide specialized technical advice for all surface preparation activities, application of paints to protective coatings in general (hot galvanizing, painting, etc …)
- INFRARED THERMOHYGROMETER, for the measurement of Temperature, Humidity and Dew Point;
- BRESLER TEST KIT, for the verification of contaminating elements such as chlorides dissolved in water and any corrosion products in accordance with EN ISO 8502-6, EN ISO 8502-9
- Check after “dusting” on the sandblasted surface with Adhesive Tape, in accordance with UNI EN ISO 8502-3
- Test with “METHYL ETHYL KETONE”, for the control of Reticulation according to ASTM D4752 standard
- ISO COMPARATOR “GRIT”, for visual-tactile control of the profile of the sandblasted surface (Roughness) in accordance with UNI EN ISO 8503-2, 8503-1,12944-4
- ROUGHNESS CHECK, for checking the roughness of the sandblasted surface in Ra, Rz, Ry
- CHECK DEGREE OF CLEANLINESS, through comparison between Photographic standards in accordance with ISO 8501-1
- WET FILM THICKNESS CHECK, in accordance with UNI EN ISO 2808
- DRY FILM THICKNESS GAUGE, in accordance with UNI EN ISO 2808, ISO 19840
- “X TEST” ADHESION TESTS in accordance with ASTM D3359
- PIG “Painting Inspector Gauge”, destructive test for the control of the thickness of the single coating on a complete Painting cycle.